The discovery and production of phosphorusPeter E. Childs UL
Put 21st. century man on an island or in a jungle without matches or a lighter and watch them struggle to create fire! We have lost the traditional skills of flint and tinder, of a friction stick, or one of the other time-honoured methods. It would now take us a long time, much experimentation (and even then we might well fail) to produce a flame. We would give anything for a simple box of matches, that humble, unsung product of the chemist and the chemical industry that has revolutionised everyday life around the world. How many times have you needed a light today - for the fire, the cooker or (unfortunately) a cigarette? We would be lost without a box of matches or a lighter, and none of us could make either of them from scratch! In this series of articles I want to trace the history of phosphorus and the friction match, and the contribution the chemical match has made to our comfort. Sadly, no matches are made any longer in the United Kingdom or Ireland - in Ireland Maguire & Patterson stopped manufacture in 1982 and in the U.K. Bryant & May closed its last match factory in 1997. The matches we buy now are made in Sweden or perhaps China (who seem to make almost everything these days). The match factories closed because of the competition from the disposable lighter, that awkward creation of plastic, metal and butane which as often as not burns one's fingers as one tries to light something. But its convenience has almost killed off the humble match, that matchless triumph of applied chemistry.
The burning brand - Brand discovers phosphorus!The story of the match goes back to the discovery of phosphorus by Hennig Brand (or Brandt) in 1669, immortalised in the painting by Joseph Wright of Derby (see below) and is one of the many legacies to civilisation of that despised domestic product, urine.
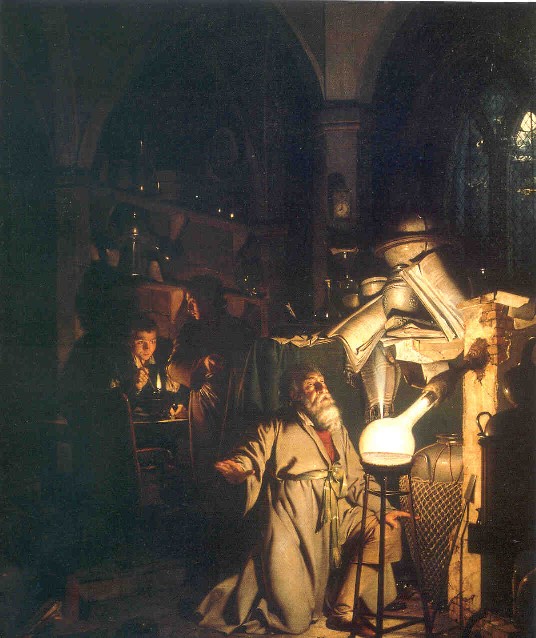
"More than 300 years ago, in 1669, Hennig Brand, a Hamburg alchemist, like most chemists of his day, was trying to make gold. He let urine stand for days in a tub until it putrified. Then he boiled it down to a paste, heated this paste to a high temperature, and drew the vapours into water where they could condense - to gold. To his surprise and disappointment, however, he obtained instead a white, waxy substance that glowed in the dark.
Brand had discovered phosphorus, the first element isolated other than the metals and non-metals, such as gold, lead and sulphur, that were known to the ancient civilisations. The word phosphorus comes from the Greek and means light bearer.
Brand (also known as Dr. Teutonicus) evaporated urine and so produced ammonium sodium hydrogenphosphate (microcosmic salt), which on heating produces sodium phosphite. When heated with carbon (charcoal) this decomposed to produce white phosphorus and sodium pyrophosphate.
1. (NH4)NaHPO4 —› NaPO3 + NH3 + H2O
2. 8NaPO3 + 10C —› 2Na4P2O7 + 10CO + P4
Brand's discovery was an accident but his discovery of phosphorus mirabile would turn out to be more valuable than gold in the future, for this 'cold fire' would enable inventors to produce fire on demand, an unimaginable achievement to Brand's contemporaries. Brand had tried to keep the method secret but he had sold the 'secret' to the German chemist, Krafft, who showed off the new wonder substance around the courts of Europe where Robert Boyle saw it in London. The secret that it was made from urine leaked out and first Johann Kunckel in Sweden (1678) and later Boyle in London (1680) also managed to make phosphorus.
Robert Boyle had seen samples of Brand's phosphorus exhibited in London and he eventually worked out a method to make phosphorus from urine in 1680, improving on Brand's process by using sand.
3. 4NaPO3 + 2SiO2 + 10C —› 2Na2SiO3 + 10CO + P4
Notice that Boyle's improved method (eqn. 3) liberates all the phosphorus in the sodium phosphite. One of Boyle's assistants, Ambrose Godfrey Hankewitz, later set up in business making the new, wonder material. He charged 50/- an ounce for this new scientific curiosity. Robert Boyle was the first to use phosphorus to ignite sulphur-tipped wooden splints, forerunners of our modern matches, in 1680.
Boyle called the material 'icy noctiluca' (cold light) and examined its properties in a systematic way, which Brand and co-workers had not. To them it was just an interesting and profitable curiosity. Interestingly white phosphorus became known as English or Boyle's phosphorus to distinguish it from other luminescent materials, which were all called 'phosphorus'. Over the years these other names have vanished leaving only elemental phosphorus.
In 1769 J.G. Gahn and C.W. Scheele2 showed that calcium phosphate (Ca3(PO4)2) is found in bones and obtained phosphorus from bone ash. Lavoisier recognised phosphorus as an element in 1777. Bone ash became the major source of phosphorus until the 1840s. Phosphate rock, a mineral containing calcium phosphate, was first used in 1850 and following the introduction of the electric arc furnace in 1890 this became the only source of phosphorus. Phosphorus, phosphates and phosphoric acid are still obtained from phosphate rock. A major use for phosphate rock is for making phosphate fertilizers (but that's another story.)
Albright and WilsonAlbright & Sturges started making phosphorus in the UK in 1844 and are still one of the major world producers of phosphorus chemicals3. The company, located at Oldbury in the 'Black Country', was founded by Arthur Albright (1811-1900), a Quaker. The Quakers, a nonconformist Christian group, became very influential in business and industry in the 18th. and 19th. century, partly because they were prevented from entering traditional occupations4. At 16 Arthur was apprenticed to a chemist-and-druggist uncle in Bristol, the start of many a chemical career in the 19th. century. In 1840 he became a partner in the firm of John & Edmund Sturges of Birmingham, manufacturing chemists, and in 1844 he persuaded his partner to start making phosphorus, then coming into use for making matches. It cost 5/- a pound and most of it was imported. The raw material was bone ash, imported from South America and later from eastern Europe. The first factory was in Selly Oak, Birmingham. The company moved to Oldbury and erected a new factory in 1850, and the first phosphorus was made at Oldbury in 1851. Oldbury was already a centre of chemicals, with local supplies of coal and a good canal and rail transport system. A contemporary writer, Walter White, wrote in 1860 of a visit to Oldbury:
"Among the chimneys rise those of a phosphorus factory, where, at some risk, and at a fierce temperature, phosphorus is extracted from bones, in such quantities that England, which used to import, now exports the article, sending many tons to Vienna and receiving it back on the end of matches by hundreds and millions every week. One pound of phosphorus, worth about two-and-nine-pence, suffices to charge a million of matches."5
Albright said that he thought of making phosphorus because Sturges was already supplying the 'twin sister' of phosphorus used in matches, namely chlorate of potash (KClO3). He thought he could make it cheaper than on the Continent because of the good supplies of cheap coal in the Black Country. At first the price of phosphorus was 7s.6d. a lb, but this came down to 6d. a lb. by the 1880s, as the economies of scale started to produce fruit. England became by 1860 a net exporter of phosphorus. The partnership with Sturges was dissolved in 1855 and in 1856 John Edward Wilson (another Quaker) joined Albright in partnership and the firm was incorporated as Albright & Wilson in 1856. He supplied the administrative acumen to support Albright's chemical genius: "if Arthur struck the spark, John Edward blew it to a flame; and it was his wise and constant tending that kept it burning ever more brightly."6 Wilson ensured that the new company was run profitably with as little waste as possible, so that it survived and prospered while 25 other phosphorus works opened and closed in Oldbury in as many years.
Initially the raw material for phosphorus production was animal bones, later replaced by mineral phosphates.
The bones or rock were dissolved in sulphuric acid to give phosphoric acid and calcium sulphate as a by-product. The acid was concentrated, mixed with 25% of its mass with carbon, dried in iron pots to a black powder and then distilled in clay retorts. Phosphorus distilled over and was condensed into 25-30 lb. blocks called 'cheeses'. After refining and casting into sticks (all under water to prevent it catching fire), the product was shipped, again under water, to the end users. In the 1890s this original batch process was superseded by the continuous electrothermic process. Cheap electricity rather than coal was now the key to cheap phosphorus and by 1920 production had ceased at Oldbury and Albright & Wilson transferred their production to Niagara Falls, in the USA and Canada.
As soon as Albright heard of Schr”tter's discovery of the safer red phosphorus in 1844 he bought the patent and started to develop a safe production process. He was successful and the Oldbury works started making red (or amorphous) phosphorus in 1851 by heating white phosphorus at a controlled temperature in a closed iron pot. The problem of making reliable matches using red phosphorus was yet to be solved, but eventually Albright's efforts to make a safer form of phosphorus was to protect to health of match makers around the world. Production of red phosphorus did not expand until a successful safety match was invented
So am I reading this wrong or can phosphoric acid and carbon be used to make white phosphorus which can then be used to make red phosphorus.
Surely its not that easy is it?